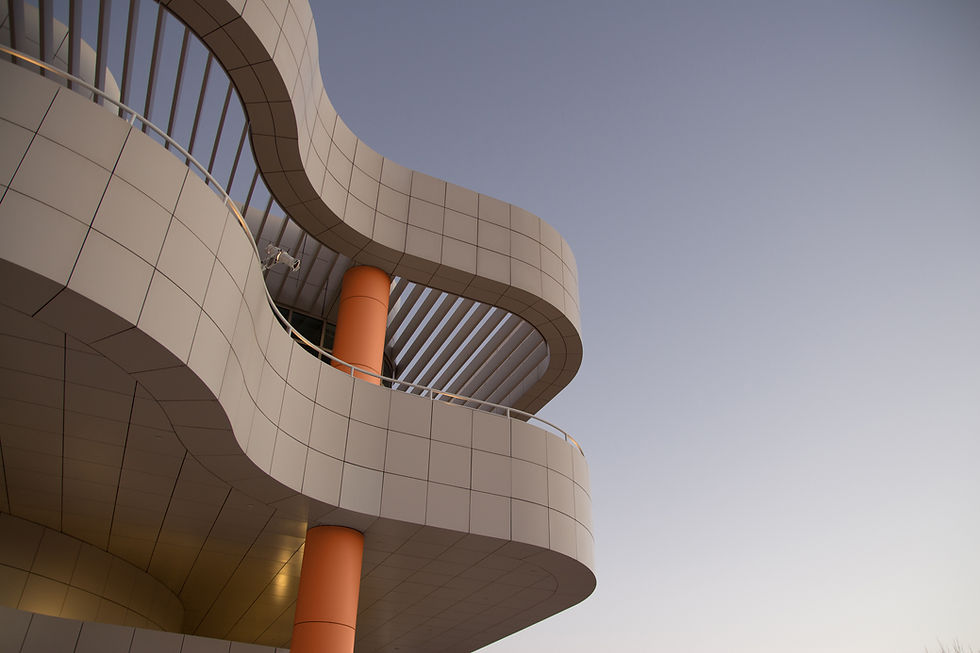
Refractory Anchors: The Silent Supporters of Industrial Furnaces
In the demanding world of high-temperature industrial furnaces, many components work together to keep operations running smoothly. Among these, refractory anchors play a quiet yet crucial role, stabilizing and supporting the refractory lining—the insulation layer that protects the furnace walls from extreme heat, mechanical stress, and corrosive environments. While often hidden from view, refractory anchors are essential to the durability, efficiency, and safety of industrial furnaces. Let’s explore what makes these anchors so indispensable.

The Role of Refractory Anchors
Refractory anchors act as the backbone of furnace linings, securing the insulation material to the walls, roof, and floors of furnaces, kilns, and reactors. This reinforcement prevents the refractory lining from sagging, cracking, or falling, especially in high-temperature settings where stability is critical. By anchoring the lining, these supports help prolong furnace life, reduce downtime, and improve performance.
Material Matters: Choosing the Right Anchor
Refractory anchors come in various materials, including stainless steels, Inconel, and even ceramic alloys, each suited to specific temperature ranges and operational environments. Stainless steel anchors, like 304, 310, or 330, are popular choices for general high-temperature applications, while more advanced alloys handle extreme or corrosive conditions. The choice of material is essential, as the wrong anchor can degrade quickly, compromising the entire refractory system.
Types of Refractory Anchors
Depending on the furnace design and lining thickness, various types of refractory anchors are used. Common designs include V-shaped, Y-shaped, and U-shaped anchors, each providing different levels of support and load distribution. For thicker linings, dense-metal ceramic anchors offer excellent durability and performance. Custom designs are also available for specialized applications, ensuring a perfect fit with unique furnace requirements.
Installation Precision for Longevity
Installing refractory anchors requires precise spacing, alignment, and welding to ensure the lining remains firmly attached and supported. Proper spacing helps prevent stress points that can lead to premature cracking or detachment. Weld quality is equally important, as weak or poorly executed welds can cause anchors to break free under high temperatures and mechanical loads. Installation accuracy directly influences the lifespan of the furnace lining, highlighting the importance of skilled labor and detailed planning.
How Anchors Withstand Thermal Expansion
Industrial furnaces experience significant thermal expansion and contraction due to rapid temperature fluctuations. Refractory anchors are designed to accommodate these changes, allowing the lining to expand and contract without breaking away from the structure. Anchors made from materials with compatible thermal expansion properties are crucial for this resilience, helping the entire lining system withstand daily operational stresses.
Maintenance of Refractory Anchors
While designed for durability, refractory anchors are still subject to wear over time, especially in high-stress environments. Regular inspections of the lining and anchors help detect early signs of degradation, allowing for timely maintenance or replacement. Ensuring anchor integrity can prevent more extensive repairs and downtime, helping maintain a safe and efficient furnace operation.
Why Refractory Anchors Are Indispensable
Although refractory anchors may go unnoticed, their role in industrial furnace performance is undeniable. By securing the refractory lining, they ensure the furnace can withstand extreme temperatures, mechanical impacts, and chemical exposure. Without reliable anchors, furnace linings would degrade quickly, leading to higher operational costs, increased maintenance, and potential safety risks.
Conclusion
Refractory anchors are indeed the silent supporters of industrial furnaces, providing essential stability and durability to the refractory lining. Their role in maintaining the structural integrity of furnaces, kilns, and reactors under intense conditions cannot be understated. Through proper material selection, precise installation, and regular maintenance, refractory anchors contribute significantly to the longevity and efficiency of industrial furnaces, enabling industries to operate with greater reliability and lower costs. In the demanding world of high-temperature environments, refractory anchors truly are the unsung heroes.
Frequently Asked Questions
What role do refractory anchors play in industrial furnaces?
Refractory anchors secure the insulation lining to the furnace structure, preventing sagging, cracking, or falling of the lining and ensuring structural stability in high-temperature environments.
How do you choose the right material for refractory anchors?
What types of refractory anchors are available?
Why is precise installation important for refractory anchors?
How do refractory anchors handle thermal expansion?