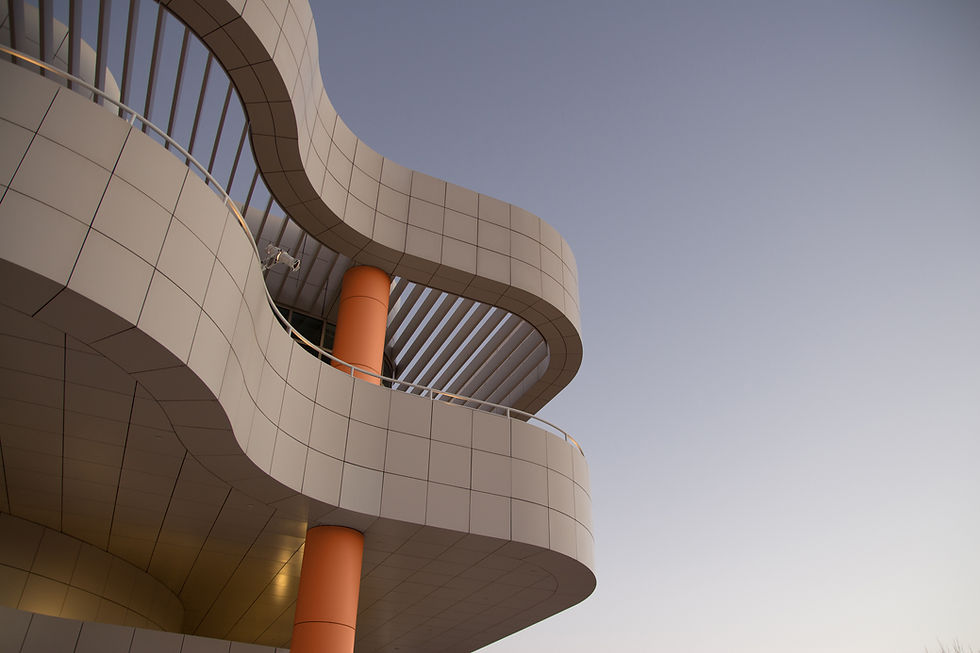
Maximizing Efficiency with Ceramic Fiber Modules: The Next Generation of High-Temperature Insulation
In today’s industrial landscape, energy efficiency and operational reliability are critical to success. For industries that operate in extreme temperature environments, effective insulation is not just a choice, but a necessity. Ceramic fiber modules have emerged as an innovative solution for high-temperature insulation, offering exceptional thermal properties, ease of installation, and enhanced performance over traditional insulation materials. In this blog, we explore the advantages, applications, and future potential of ceramic fiber modules in optimizing industrial processes.

What Are Ceramic Fiber Modules?
Ceramic fiber modules are pre-engineered insulation units made from folded or stacked layers of ceramic fiber blankets. These modules are designed to simplify the installation process, reduce heat loss, and increase the overall efficiency of high-temperature furnaces, kilns, and other thermal processing equipment. Their modular design allows for easy attachment to furnace linings and walls, making them an ideal solution for a wide range of high-temperature applications.
Key Benefits of Ceramic Fiber Modules
Superior Thermal Insulation: Ceramic fiber modules are highly effective at insulating against extreme temperatures, often ranging between 1000°C and 1600°C. Their low thermal conductivity minimizes heat transfer, helping industries retain heat within the system and significantly reducing energy consumption.
Effortless Installation: Unlike traditional ceramic fiber blankets, which require careful placement and sealing, ceramic fiber modules are pre-constructed and can be directly anchored to furnace linings. This modular design reduces installation time and labor costs, while also ensuring a more consistent and reliable insulation layer.
High Durability and Longevity: Ceramic fiber modules are resistant to mechanical wear, thermal shock, and chemical corrosion, which gives them a longer lifespan compared to other insulation materials. Their ability to withstand harsh industrial conditions makes them a cost-effective solution for long-term operations.
Energy Efficiency: By minimizing heat loss and maintaining consistent temperatures, ceramic fiber modules contribute to energy efficiency in industrial processes. The reduced thermal mass means that furnaces can heat up and cool down faster, saving valuable time and energy during operations.
Flexibility and Versatility: Ceramic fiber modules come in various sizes and configurations, allowing them to be customized for specific applications. Their flexibility ensures that they can be tailored to fit any industrial furnace or kiln design, making them ideal for both new construction and retrofitting existing systems.
Reduced Maintenance and Downtime: The robust nature of ceramic fiber modules means less frequent maintenance is required, reducing downtime and keeping production running smoothly. Their easy removal and replacement also contribute to lower maintenance costs over time.
Applications of Ceramic Fiber Modules
Due to their exceptional performance in high-temperature environments, ceramic fiber modules are widely used across a range of industries:
Steel and Metal Processing: In steel mills and foundries, ceramic fiber modules are used in furnace linings to retain heat during metal melting, casting, and annealing processes. Their ability to withstand extreme heat ensures that the furnaces operate efficiently and at optimal temperatures.
Glass Manufacturing: Glass production requires precise temperature control. Ceramic fiber modules help maintain the high temperatures needed for melting and forming glass, ensuring energy-efficient production and minimizing heat loss in the process.
Petrochemical and Chemical Processing: The petrochemical industry relies on ceramic fiber modules for reactors, reformers, and other high-temperature equipment. Their chemical resistance and durability make them ideal for withstanding aggressive environments while optimizing heat insulation.
Ceramic and Kiln Operations: Ceramic fiber modules are commonly used in kilns for pottery, ceramics, and brick production. Their insulation properties allow for even heating and cooling, improving product quality and reducing energy consumption during firing.
Power Generation: In power plants, ceramic fiber modules are used to insulate boilers, turbines, and exhaust systems. By improving the energy efficiency of these critical systems, power plants can operate more sustainably and reduce their carbon footprint.
The Future of Ceramic Fiber Modules
As industries continue to focus on reducing energy consumption and environmental impact, ceramic fiber modules are poised to play a crucial role in advancing thermal efficiency. With ongoing innovations in materials science, ceramic fiber modules are becoming even more versatile and effective at insulating in extreme conditions. Their ease of installation and customization options ensure they remain a top choice for industries looking to upgrade or enhance their thermal insulation systems.
Why Choose Ceramic Fiber Modules?
Ceramic fiber modules offer numerous advantages over traditional insulation materials. Their ability to provide superior thermal insulation, combined with reduced installation time and low maintenance requirements, makes them a highly cost-effective solution for industries operating in high-temperature environments. By choosing ceramic fiber modules, companies can enhance energy efficiency, extend the lifespan of their equipment, and lower overall operational costs.
Conclusion
Ceramic fiber modules are revolutionizing the way industries approach high-temperature insulation. With their superior thermal properties, ease of installation, and long-lasting durability, these modules provide a solution that not only maximizes energy efficiency but also minimizes costs over time. Whether you’re working in steel manufacturing, glass production, petrochemical processing, or any other high-temperature industry, ceramic fiber modules are a next-generation solution for improving performance and sustainability.
By embracing the benefits of ceramic fiber modules, industries can significantly reduce energy waste, protect critical equipment, and enhance their operational efficiency, ensuring long-term success in an increasingly competitive global market.
Frequently Asked Questions
What are ceramic fiber modules made of?
Ceramic fiber modules are made from folded or stacked layers of ceramic fiber blankets, which are pre-engineered into modular units. These modules are designed for easy installation and provide excellent thermal insulation for high-temperature applications.
What temperature ranges can ceramic fiber modules handle?
How do ceramic fiber modules improve energy efficiency?
What industries benefit most from using ceramic fiber modules?
How do ceramic fiber modules simplify installation compared to traditional insulation materials?