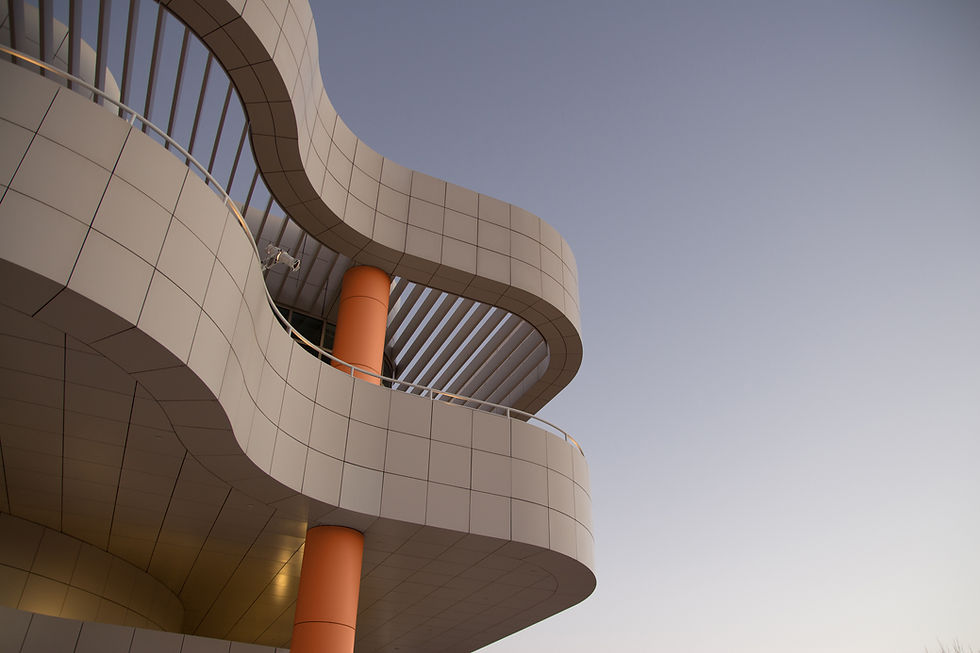
Innovations in Refractory Anchors: Trends and Technologies Shaping the Industry
In the realm of high-temperature applications, refractory anchors play a crucial role in securing linings and ensuring the integrity of industrial furnaces, kilns, and reactors. Over the years, advancements in materials and manufacturing technologies have revolutionized the refractory anchor industry, allowing for better performance, longevity, and adaptability to diverse operating conditions. In this blog, we will explore some of the key trends and emerging technologies shaping the future of refractory anchors.

Advanced Material Alloys for Enhanced Durability
The harsh environments in which refractory anchors are used demand materials capable of withstanding extreme temperatures, chemical corrosion, and mechanical stress. Innovations in material science have led to the development of advanced alloys with superior properties. High-nickel alloys, chromium-based materials, and specially formulated stainless steels have significantly improved the durability and lifespan of refractory anchors. These advanced materials not only enhance performance but also reduce the frequency of maintenance, cutting down operational costs in the long term.
Customization and Precision Manufacturing
The demand for more precise, application-specific solutions has driven the development of highly customizable refractory anchors. Modern manufacturing techniques, such as CNC machining and 3D modeling, allow for the production of anchors tailored to the exact specifications of various refractory linings. This precision ensures optimal fit, minimizing the risk of premature failure or thermal cycling issues. Moreover, manufacturers are leveraging rapid prototyping to test and validate new designs before full-scale production, accelerating the innovation process.
Innovative Anchor Designs
New design innovations are addressing some of the most common challenges in refractory applications, such as thermal expansion, cracking, and material displacement. Patented anchor designs now include flexible configurations that allow for controlled movement and thermal expansion without compromising the integrity of the lining. These designs improve the thermal shock resistance of the system, increasing the overall efficiency and safety of high-temperature processes. Furthermore, modular anchor systems enable faster installation and easier replacement, minimizing downtime during maintenance cycles.
Integration of Digital Technologies
As part of the broader Industry 4.0 transformation, digital technologies are starting to make an impact on refractory anchor manufacturing. Sensors and smart monitoring systems can now be integrated into refractory linings, providing real-time data on the performance of anchors in extreme environments. Predictive maintenance, enabled by these digital tools, helps operators anticipate potential failures and schedule maintenance before catastrophic issues arise, significantly extending the lifespan of the anchors and reducing unplanned downtime.
Sustainability and Green Manufacturing Practices
As sustainability becomes a core focus for industries worldwide, the refractory anchor industry is also adopting greener practices. Manufacturers are exploring eco-friendly materials, such as recycled metals and low-carbon alloys, to reduce the environmental impact of production. Additionally, energy-efficient manufacturing techniques, including electric furnaces and low-waste processes, are being implemented to lower carbon footprints. These efforts align with the growing demand for sustainable solutions in high-temperature industrial applications.
Future Outlook: What’s Next?
The future of refractory anchors lies in the continued convergence of material science, digitalization, and sustainable practices. As industries push the boundaries of what’s possible in high-temperature environments, manufacturers will need to develop even more resilient and adaptable anchor systems. With advancements in AI-driven design, smart materials, and further integration of IoT technologies, the next decade will likely see refractory anchors becoming smarter, more efficient, and increasingly specialized.
Conclusion
Refractory anchors are a vital component in ensuring the safety and performance of high-temperature systems. The industry’s ongoing focus on innovation is driving significant improvements in durability, design flexibility, and operational efficiency. As new trends and technologies emerge, manufacturers and operators alike will benefit from reduced costs, enhanced safety, and longer service life in some of the most demanding industrial environments.
By staying at the forefront of these innovations, businesses can position themselves to take full advantage of the next generation of refractory anchor technologies, ensuring they remain competitive in an ever-changing industrial landscape.
Frequently Asked Questions
What role do refractory anchors play in industrial applications?
Refractory anchors are critical components used to secure refractory linings in high-temperature industrial systems like furnaces, kilns, and reactors. They help maintain the integrity of the lining by resisting thermal expansion, mechanical stress, and corrosion, ensuring stable and efficient operation in extreme environments.
How have material innovations improved the performance of refractory anchors?
What are some recent design innovations in refractory anchors?
How is digital technology influencing the refractory anchor industry?
In what ways is sustainability impacting the manufacturing of refractory anchors?